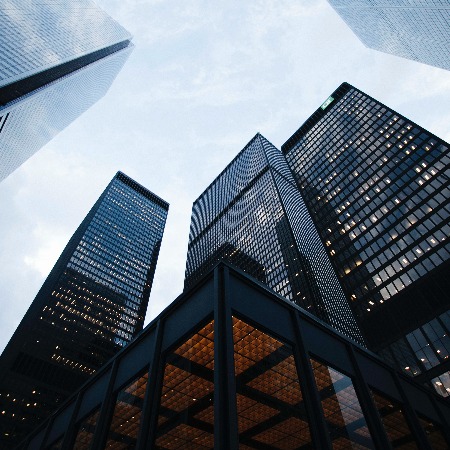
Owner’s Objectives: It Is Critical To Be Clear From the Start
[fa icon="calendar'] Jun 2, 2021 1:32:00 PM / by John R. Manning, PE, CCM, LEED
For owners and Property Managers, one of the most difficult aspects of construction disputes is the mismatch between what the owner wanted and what the architect or contractor delivered. It is especially troublesome when a review of the project reveals that the problem could have been avoided with clear communication about the owner’s goals for the project. Because of the problems that arise when the owner’s objectives are not met, the most important role of the owner’s representative is to ensure that the goals and objectives of the project are clear.
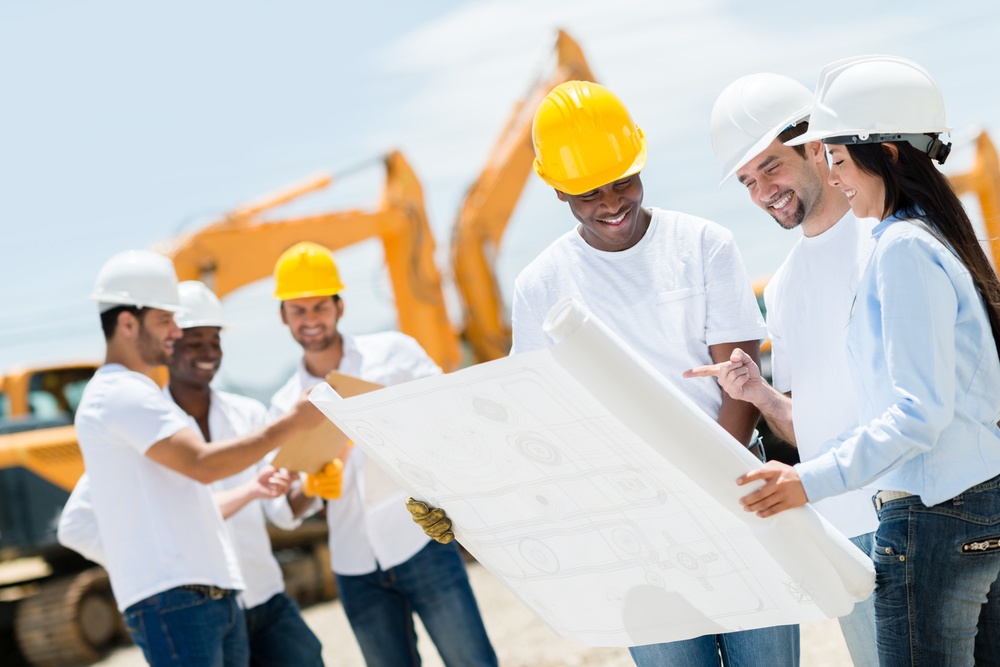
Selecting a Design Consultant; A Guide for Owners and Property Managers
[fa icon="calendar'] Mar 22, 2021 7:15:00 AM / by Peter A. Byrne, PE
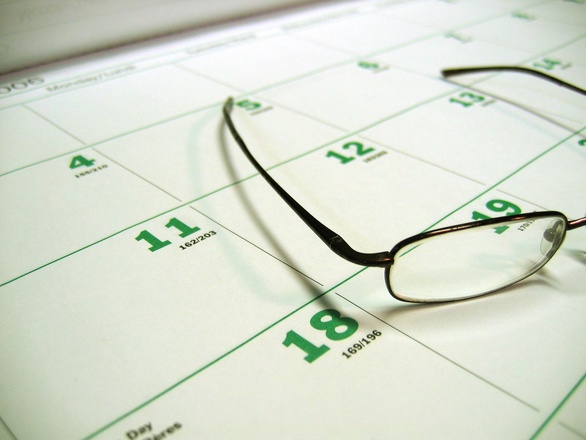
How to Avoid Broken Construction Projects and Late Schedules
[fa icon="calendar'] Mar 3, 2021 10:15:00 AM / by Peter A. Byrne, PE
Owners have a lot of responsibility when it comes to design and construction—it is their money on the line while they turn to teams of experts to design and build the project. They are the ones who feel the brunt of any problems, which unfortunately abound in the construction industry. Despite awareness of the issues, the industry has not changed much in recent years.
McKinsey's research shows that construction projects typically take 20 percent longer to finish than the original schedule, can be up to 80 percent over budget, and frequently result in litigation.
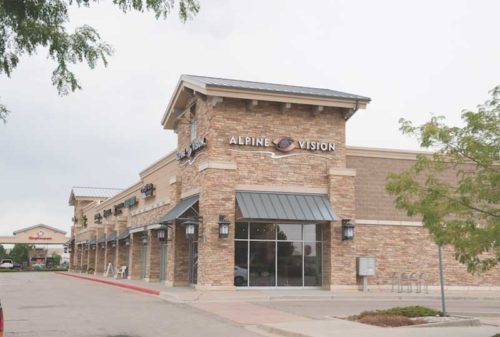
Adhered Manufactured Stone Veneer: Manufacturing performance for the winter
[fa icon="calendar'] Feb 1, 2018 10:00:00 AM / by Clark Griffith, AIA
An Adhered Masonry Veneer system (AMV) is defined as “masonry veneer of natural or manufactured stone, secured to and supported by the backing through adhesion” and are sometimes called “lick and stick” systems. The more typical masonry brick veneer system has a drainage cavity behind and the veneer is supported on itself and anchored with metal ties. Exterior AMV wall components can vary, but they are similar to a stucco system with a weather resistive barrier, scratch coat with embedded wire lath, and a finish coat of adhesive mortar.
The design and installations of AMV can be challenging since relevant building codes and industry standards are not well known or understood, and the system relies heavily on workmanship and selecting the right materials. This is particularly true when choosing a manufactured stone rather than costlier natural stone, and when used in freeze-thaw climates.
Read More [fa icon="long-arrow-right"]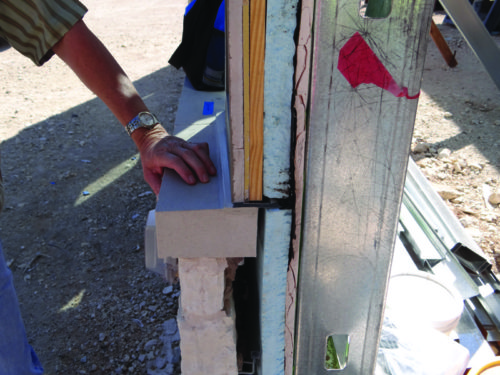
Every layer matters. A holistic approach to quality control can be useful.
[fa icon="calendar'] Dec 7, 2017 10:00:00 AM / by Mark McGivern, CSI, Aff. M. ASCE
Whose fault was it? This is a frequently asked question when an exterior wall leaks, rots, or falls down. During a construction failure investigation, contractors often highlight the defects of other trades that affected their work. Defects include those that were documented during construction but not corrected. This may be due to timing and scheduling constraints.
Often the findings from building failures are then used going forward as best practices for new construction. However, those learned best practices should not be the only guideline. Critical areas that need to be addressed include the points of intersection, as many times there are multiple layers of building materials which are put in place by various subcontractors. This step is known as a pre-covering inspection. A pre-covering inspection of each layer at each wall area would be ideal, so problems at each layer do not accumulate, influence other layers, or get concealed.
The following article looks at examples of pre-covering inspection criteria to illustrate the influence each layer may have. Continue reading….
Read More [fa icon="long-arrow-right"]
Man with Walnut Allergy Dies on Construction Site
[fa icon="calendar'] Nov 30, 2017 10:00:00 AM / by Clark Griffith, AIA
Alberta Occupational Health and Safety investigators are looking into the death of an Edmonton man with a nut allergy who died after visiting a work site where walnut shells were used to blast paint off walls.
Recently alternatives to sandblasting including the use of walnut shells, coconut shells and corn cobs have been widely used in the construction industry over the last decade.
Read More [fa icon="long-arrow-right"]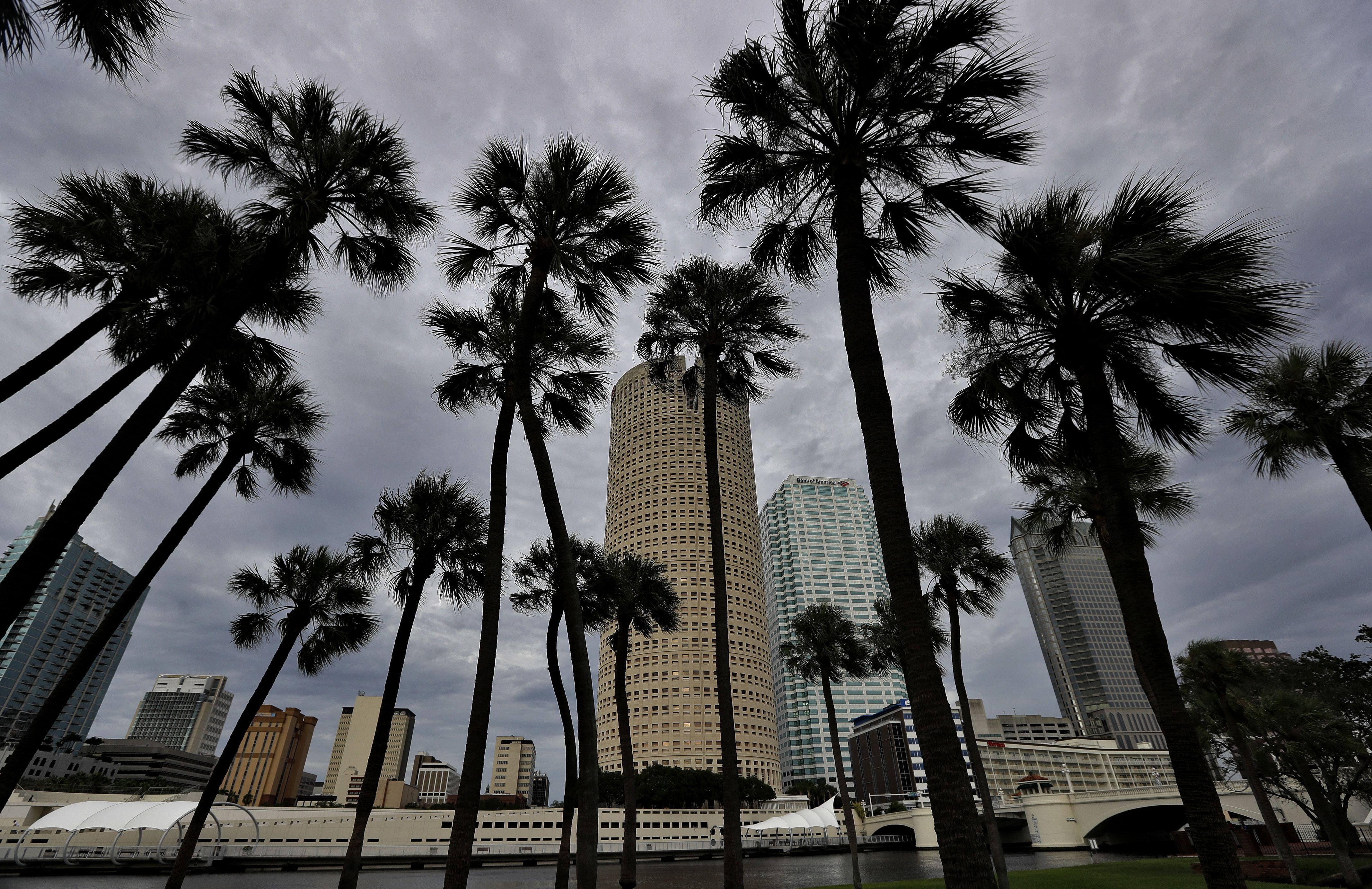
Stricter Building Codes Saved Florida’s Commercial Buildings from Irma’s Wrath
[fa icon="calendar'] Nov 28, 2017 10:00:00 AM / by Mark McGivern, CSI, Aff. M. ASCE
Hurricane Irma bore down hard on single-family homes, severely damaging many. At the end of September residential insurance claims had been cited around a half-million. The story, however is quite different for commercial and industrial buildings where insurance claims had been cited around 25,000.
This is mainly due to the stricter building codes that were put in place following the wrath of Hurricane Andrew in 1992. “Designed to withstand a Category 5 hurricane with winds of 175 mph, the Florida building code is the accepted benchmark for hurricane protection nationally.”
“Florida significantly strengthened its defenses after hits from past major hurricanes, and those improvements were instrumental in helping the state weather this potentially devastating storm,” Levy notes. “As a result, damage to Florida commercial real estate is relatively minor outside of the Keys.”
Read More [fa icon="long-arrow-right"]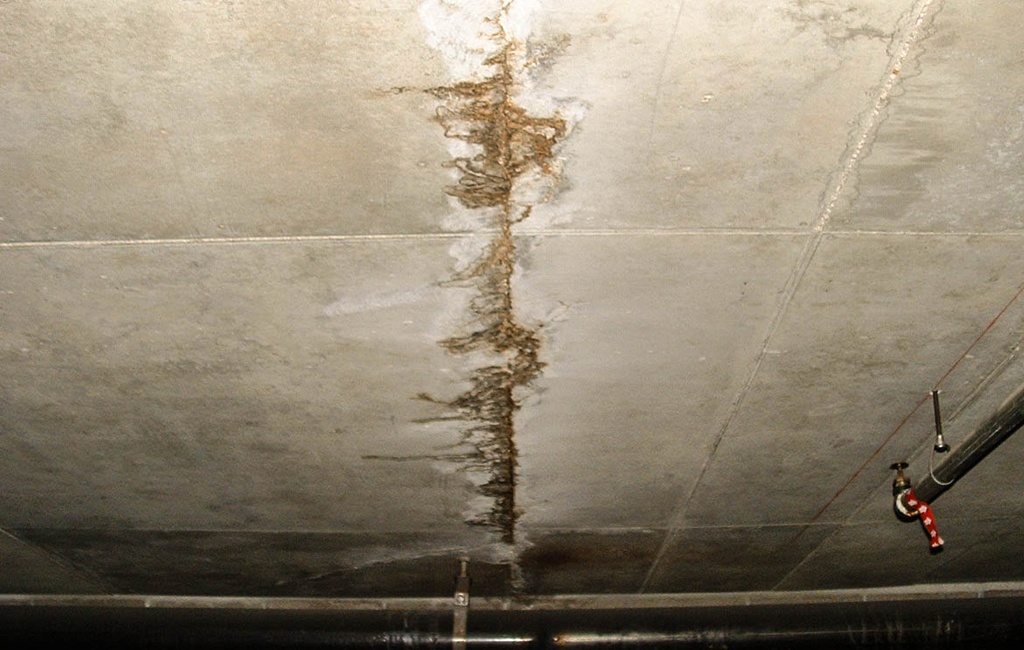
Water Damage During Construction
[fa icon="calendar'] Oct 11, 2017 3:55:00 PM / by Robert Pfeifer, AIA
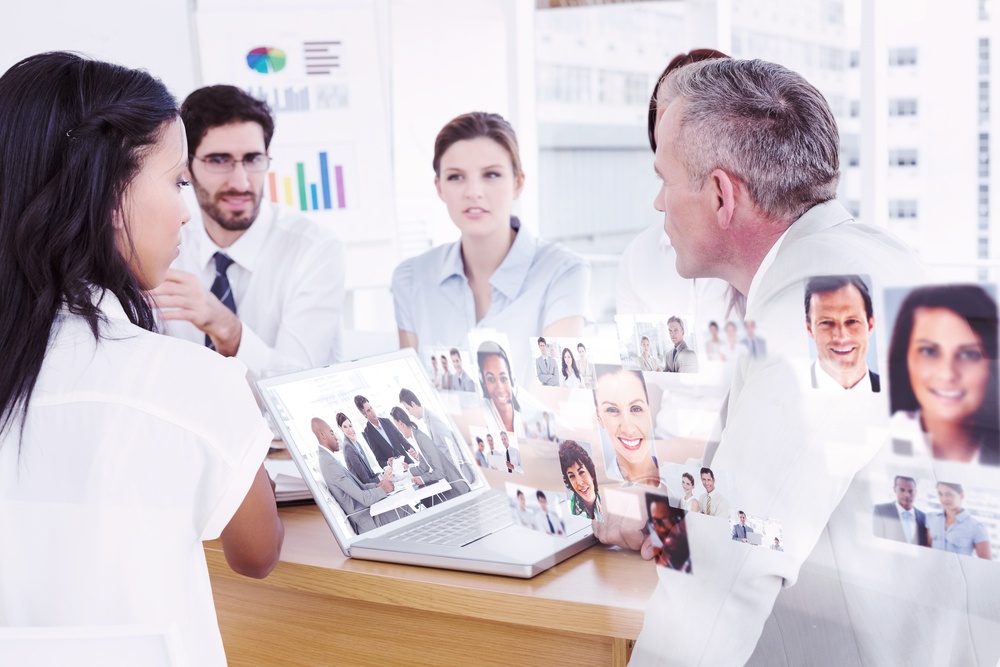
If All Else Fails – Communicate Effectively!
[fa icon="calendar'] Aug 16, 2017 12:37:00 PM / by John R. Manning, PE, CCM, LEED
Many projects often bring to mind the famous line from Cool Hand Luke – “What we've got here is a failure to communicate.”
One of the definitions of communication from Merriam Webster Dictionary is “a technique for expressing ideas effectively.” On today’s projects, everyone on the project seems to be communicating, whether that be talking, emailing and/or sending correspondence, but the reality is that no effective communication is occurring. Many times, project participants are overwhelmed with the amount of correspondence and get extremely defensive of their positions, especially if they miss something. We may not have a failure to communicate but it appears many times that we have a failure to communicate EFFECTIVELY.
So how do we address this failure to communicate effectively??? I still remember one of my first classes on public speaking where the professor laid out a simple yet effective outline for a speech. He said in the Opening you tell them what you plan on speaking about; then in the Body you tell them what you are speaking about; and, finally, in the Conclusion you tell them what you told them! This has been shown to be an extremely effective means of communicating in speech to inform someone of a topic.
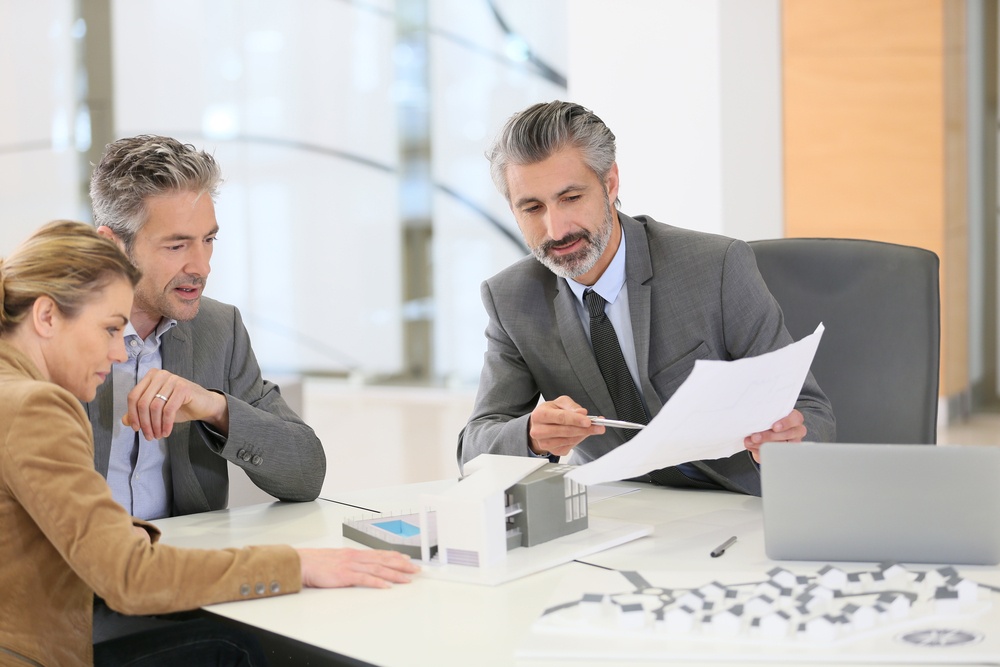
The Importance of a Quality Management Plan and Why it Should be Completed Early!
[fa icon="calendar'] Aug 8, 2017 10:30:00 AM / by John R. Manning, PE, CCM, LEED
Quality on a project, many times, is one of the last considerations for an Owner whom usually focuses first on cost and then schedule.
At the end of the day, the Quality of a built project is extremely critical for a lot longer than the time it took to design and build it. In the Project Management Plan, there should be a Quality Management Plan portion. In that segment the Project Manager should outline who will be responsible for delivering quality on a project. This starts first with a good design. One of the first steps the Owner’s Representative can do is to develop a Differentiation Document that clearly outlines who will be responsible for what in a Project, similar to the following example of a site and pool area development.